When looking for a manufacturer to continue producing your OEM products, not just any partner will do. Several critical factors will directly impact your bottom line for better or worse, depending on which manufacturer you choose. Among these factors is the type of internal production model a manufacturer uses to process orders. The answer you’re looking for is cellular manufacturing. Here’s why:
Cellular vs. Traditional Manufacturing 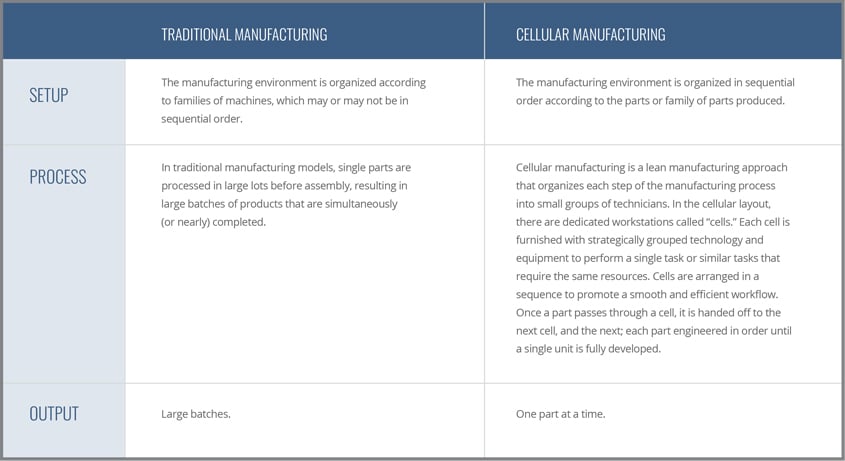
Advantages of Cellular Manufacturing
Faster Changeover Process: The changeover process is a series of steps that a manufacturer takes to transition a production line for the development of a new product. This process involves switching out workers, materials, machines and technologies. Depending on the extent, changeover can cost the manufacturer significant time and money, which ultimately gets passed on to the OEM and customer. The changeover process is unavoidable, regardless of the manufacturing method. However, when cellular manufacturing environments are strategically configured, they can increase machine utilization, operator utilization and production rate while reducing setup time to cut down on ancillary costs.
Less Waste: Bulk production that takes place out of sequence makes it easy to overproduce parts before the next step in the manufacturing process is ready. Because cellular manufacturing processes produce a product one part at a time, in a logical order, the risk for material and resource waste is far less, as is work-in-progress (WIP) inventory.
Shorter Cycle Time: The optimized one-piece workflow of a cellular manufacturing system eliminates waiting time between batches. Paired with faster production processes, less waste and lower risk of defects, a company that has implemented cellular manufacturing often experiences a shorter cycle time without compromising output volume.
Higher Quality Product: Defective parts or products are often the results of poor process control and communication on the floor (among other factors). Once again, traditional manufacturing lines aren’t always arranged in sequential order, which segregates the people engineering the parts. Cellular environments don’t guarantee the elimination of defects, but they do significantly reduce the risk of a defect by allowing technicians to identify issues sooner and make corrections before they become costly mistakes. A problem discovered in a single part is far easier to fix than a problem discovered in a large batch of parts.
In addition to providing customers with superior quality cable assemblies and connectors, iCONN Systems is committed to building value into every product and service we offer. From reengineering, prototyping and in-house certifications to our lean, cellular manufacturing process, we don’t just deliver on our promises, we maximize your investment with us. Learn more about our custom engineering process.