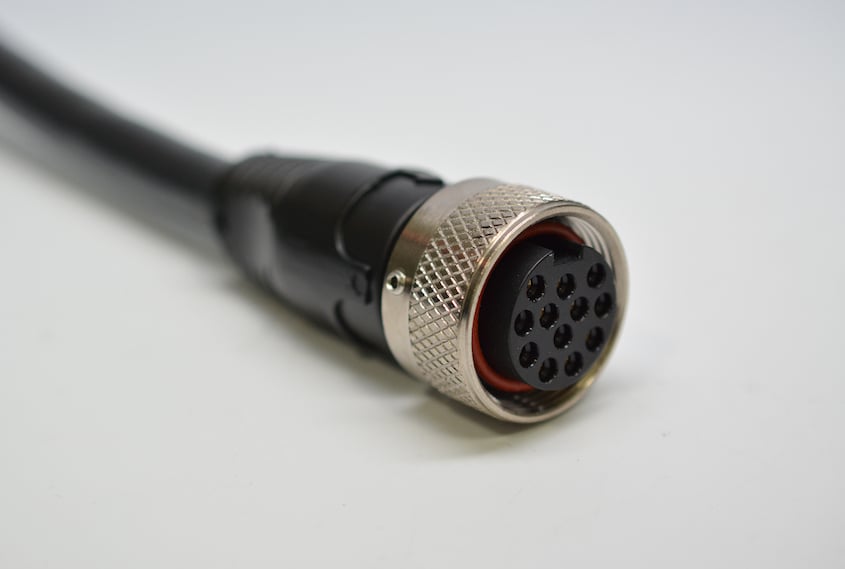
Few details will influence a product's success as significantly as its electrical design. Customers often need turnkey solutions that are both rugged and field-installable. While more affordable off-the-shelf connectors can meet a variety of application specifications, it's not uncommon for this combination of attributes to require customization, which may increase the upfront cost of ownership.
Custom circular connectors may cost more upfront but can significantly enhance lifespan, reliability and usability, making them more cost-effective. This article will help you understand your many options for power and data connectors and how specific design details can impact lead time, cost of ownership and ROI.
Understanding all factors associated with developing, scaling and manufacturing a customized part can help product teams optimize time and expenses.
Circular Connectors vs. Rectangular Connectors
All electrical connectors come in two basic shapes – circular or rectangular. Both bodies share a number of similar performance characteristics, but certain design details set them apart. Shape, in particular, plays a significant and often underappreciated role in a connector's performance and reliability.
Rectangular Connectors
Rectangular connectors have corners that create more surface area compared to circular connectors. This allows designers to fit more contacts into a smaller space. By nature, rectangular connectors are also modular, offering engineers more configuration flexibility. For example, you might arrange multiple single connectors side-by-side to conserve space or integrate power, coax, signal or fiber optics into a single rectangular connector.
Challenges with Rectangular Connectors
Any connector's signal or power strength depends on the stable and secure touching of two contact surfaces. Unfortunately, in some cases, users report issues with poor contact quality, resulting from either the low-quality design of the internal components or inadequate manufacturing practices that jeopardize the connector seal.
Additionally, while a boxy form can be beneficial in some regards, rectangular shapes can also create some inefficiencies. For example, a rectangular connector wastes a lot of space in low pin-count designs.
Circular Connectors
A circular connector product literally cuts corners, decreasing the diameter of the receptacle to meet spatial demands — particularly in low pin-count designs. Its cylindrical shape also provides exceptional terminal strength and a more streamlined fit, making circular connectors the preferred choice for applications involving a high potential for mechanical turbulence or impact damage.
Take food and beverage manufacturing, for example, where equipment must frequently endure high-pressure wash-downs and sterilization. Rectangular connectors (especially when configured side-by-side in close proximity) create crevices that are susceptible to debris and moisture. Without a proper seal, this can lead to oxidation, poor connectivity and cable failure.
With their sleek design and secure mechanical couplings, circular connectors can be configured to achieve exceptional IP ratings and offer better run-off, reducing the risk of corrosion, hygiene and reliability issues that can result.
Common Applications
Circular connectors are most common in free-hanging connections. While circular connectors are an obvious fit for round cabling and high-speed systems, their value can be observed in numerous applications across virtually any industry.
Challenges with circular connectors
Circular connectors are commonly viewed as more difficult and expensive to customize, especially when designing for miniaturized electronics. This is partly due to their smaller surface area, which limits the number of possible pin arrangements and makes it difficult to achieve higher levels of power or signal strength.
Additionally, circular connectors often require more ancillary pieces, which can increase the time and costs associated with parts and assembly. For example, affixing a circular connector and fortifying strength may require bulkheads, jam nuts, or flange mounts.
How Custom Circular Connectors Save Time and Costs
We use reverse engineering to create all-new high-performance product lines that help control the time and costs associated with customized circular connector projects.
Take our iMINI series, for example. The iMini product line features three unique circular connectors -- each designed to optimize pin density and placement. With cable dimensions as small as .27 inches, multiple contact configurations, up to 12 contacts and a 300V rating, this series provides product teams with an off-the-shelf, yet customizable solution that works in tight spaces and meets higher power and signal demands.
Likewise, we developed our iMate iCPC connector series to enhance the durability and performance of circular plastic connectors (CPCs) while simplifying field assembly labor.
Overmolding played an essential role in the success of this connector series, but not without its share of challenges. The overmolding process involves high degrees of heat and pressure — not ideal for certain connector parts. To overcome this challenge, we used gold-plated screw machined contacts that can withstand higher temperatures and pressures.
By improving the durability and IP rating of CPCs, we effectively reduced indirect cost factors associated with downstream maintenance. We also eliminated the pinch-point associated with mechanical strain relief (which often becomes a failure point in applications involving constant flex). Lastly, we chose to machine the mounting holes in the panel mount receptacle flange (rather than molding them), allowing us to fill customer requests as though they are standard offerings without the inventory or lead-time.
Download the full case study to learn more.
Design & Manufacturing Considerations
The growing demand for customizability has given rise to a new era of design that focuses on modularity. Modular design allows the customer to piece together a connector solution by choosing from a catalog of different parts. Rectangular connectors are often viewed as the superior choice for modular design and customization. However, circular connectors are just as versatile and adaptive with the right manufacturing partner.
Optimizing your circular connector requires a thorough understanding of the number of wires involved in the connection, the required gauge, the type of receptacle needed for the application and whether the connector needs to be field-attachable or field-installable and easily serviceable or not.
There are two main circular connector types:
1. Circular metal connectors (CMC) are all metal and feature a strong construct and secure mechanical connection.
2. Circular plastic connectors (CPC) are all plastic, making them lightweight and more resistant to extreme heat (with the right thermoplastic material).
Contact Pin Material
Contact pins are responsible for completing the electrical connection function. The quality of a connector's power or data transmission depends on the type of metal used to coat or construct contact pins. Metals have different levels of conductivity (i.e., the degree to which heat or electrical current is transmitted). Pure metals offer the highest degree of conductivity, while alloys offer lower levels.
The Conductivity of Metals - Highest to Lowest
- Silver
- Copper
- Gold
- Aluminum
- Zinc
- Nickel
- Brass
- Bronze
- Iron
- Platinum
Wire Gauge and Amperage
Wire gauge refers to a wire’s diameter, which determines its weight and the amount of electrical current it can safely carry (i.e., its electrical resistance). Amperage refers to the electric current’s strength.
Wire gauge and amperage are mission-critical details that can significantly impact performance and safety. If the gauge is too small for the electrical load, the wire can overheat. Without proper overmolding and insulation, overheating can melt through the cable jacketing and increase the risk of shock or electrical fires.
Download this guide to ensure you calculate the right ampacity.
Terminal Bond
You can affix a connector to a cable using two primary methods:
1. Crimping adjoins a wire to a wire or a wire to a terminal using a process that deforms or compresses metal parts until they form a gas-tight bond. This method is faster and simpler to perform and offers better water ingress protection. It's also more expensive due to tooling costs.
2. Soldering adjoins a wire to an electrical component by melting solder material onto the joint, thus creating a permanent bond. This method uses less tooling and is more economical but involves a high heat process (not ideal for certain inserts) and solder material that contains lead, which does not comply with RoHS requirements.
Coupling Mechanism
A mating or coupling mechanism refers to the mechanical design used to plug and unplug two circular connector ends. Generally speaking, there are three basic types of coupling mechanisms -- each with varying degrees of form and function.
Mounting
Circular connectors can be mounted in-line on a cable end or to panels or circuit boards.
Accessories
The ancillary parts and pieces of a circular connector can be divided into two categories:
- Structural:
- Installation or Mounting:
- Positioning pins
- Clamp rings
- Coupling rings
- Sealing rings
- Guide pins
- Positioning keys
- Cable clamps
- Gaskets
- Coils
- Bolts
- Screws
- Nuts
When To Choose A Circular Connector Design
When you understand the key considerations involved in designing a successful electrical assembly, choosing the right connector for your application becomes far less challenging. We recommend exploring a circular connector design if:
✅ Your product must pass an IP rating of 67 or higher.
✅ Your product must meet IEC and RoHS compliance requirements
✅ Your product has spatial limitations
✅ Your product will operate in harsh environments
✅ Your product will be exposed to corrosive environments
✅ Your product will endure above-average levels of vibration, shock, temperature or pressure.
✅ Your product requires quick and secure mating and unmating.
✅ Your product will operate in environments with high levels of EMI/RFI interference.
If you’re just starting a new project or need help defining your application specifications, the technical team at iCONN Systems is here to help. Our portfolio of circular connectors can meet even the most stringent industry requirements and application demands while controlling time and cost factors to deliver added value.
Learn more about our custom connector solutions.