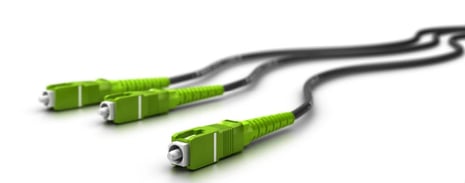
Cable and connector assemblies typically go through testing, also known as “qualification” or “verification and validation,” to ensure that the product design meets the demands of the intended application.
Understanding what the various tests are and why they’re important will help you identify the highest quality products and ensure that the cable and connector assembly you choose will perform well in the application. In this article, we will discuss the various forms of flex/bend strain relief endurance testing, which measures the mechanical resilience of a cable and connector assembly.
Strain Relief Endurance Testing
Mechanical testing evaluates a cable and connector assembly’s resilience to twisting, bending, pulling and flexing — both repeatedly and over sustained periods of time. Each stress test that a product undergoes will look for elongation, impact resistance, tensile strength and crush resistance. To evaluate these qualities, two main tests are performed.
1. The Pull Force Test
A pull force test challenges the strength of the cable and connector assembly joints and crimps. To perform this test, the cable is connected to a motorized pull tester and monitored as force is applied at a specified load and rate. In some cases, product teams are required to obtain verification that a cable can withstand a certain number of pounds of force without damage. In other cases, engineers test for threshold resilience.
2. The Flex/Bend Test
In most applications, a cable and connector assembly will undergo bending and flexing as it’s routed and installed or during regular use. The purpose of a flex/bend test is to ensure that cable assemblies, especially those designed to move in all directions, can do so without disruption to the transmittance of power or signal. To perform this test, the cable and connector assembly is attached by one end to a bend/flex machine. The opposite end may be tied or weighted depending on the nature of the test. The bend/flex machine continuously flexes the cable according to predetermined testing criteria for the bend radius and number of cycles.
To ensure that testing doesn’t interfere with project timelines, work with a cable and connector manufacturer that offers in-house testing for functionality, reliability and durability. Whether industry regulations require it or not, iCONN Systems, Inc., rigorously tests all cables and connectors to guarantee quality and prevent manufacturing errors from impacting our valued customers. Our testing facilities are also equipped with advanced equipment under highly controlled environments to ensure the most accurate results possible.
Learn more about our advanced cable and connector engineering and testing capabilities.